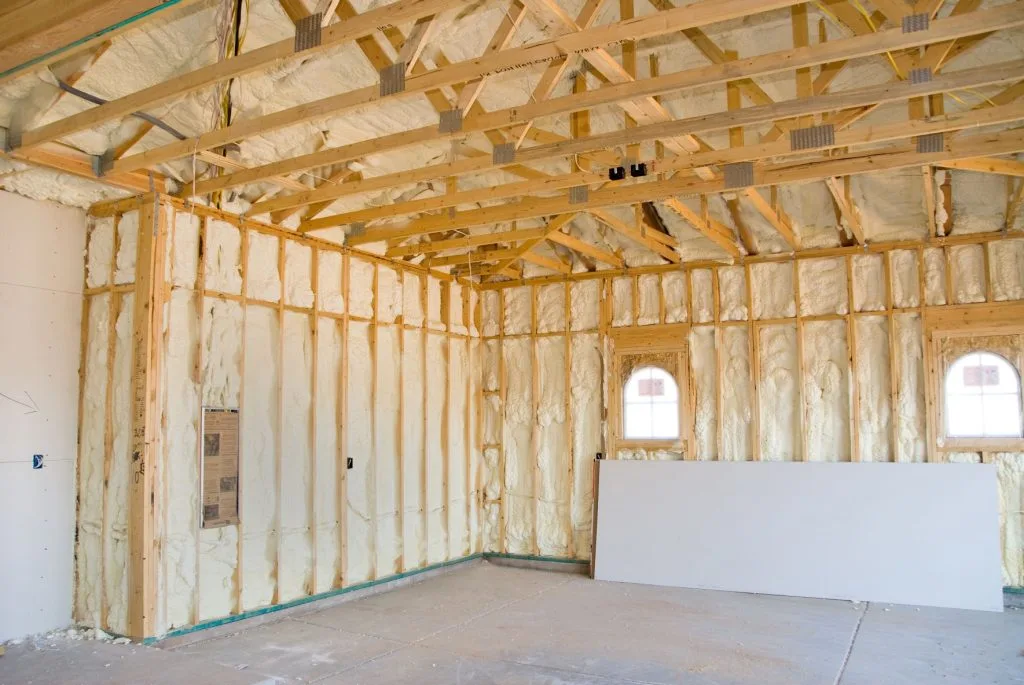
Is there any downside to spray foam insulation?
Spray foam insulation is a modern method of insulating homes and buildings that involves spraying a liquid foam material onto surfaces, where it expands and hardens into an insulating layer. This foam can be sprayed into walls, attics, crawl spaces, and other areas to create an effective thermal barrier that helps maintain indoor temperatures and reduce energy costs.
Because spray foam insulation offers so many advantages, its popularity has constantly increased. It provides excellent insulation, sealing gaps, and cracks to prevent air leakage, which can significantly improve energy efficiency. Furthermore, by limiting the introduction of pollutants, spray foam insulation can enhance indoor air quality, lessen noise transmission, and even reinforce a building's structural integrity by adding extra support.
Despite its many advantages, there are some potential downsides to consider. One concern is the initial cost, which can be higher than traditional insulation methods. Additionally, improper installation of spray foam insulation can lead to issues such as off-gassing of chemicals or uneven application, which may affect indoor air quality or the effectiveness of the insulation. However, when installed correctly by trained professionals, spray foam insulation can be a highly effective and long-lasting solution for improving the comfort and energy efficiency of a home or building.
The installation process of spray foam insulation begins with thoroughly preparing the area to be insulated. This involves clearing any debris, dust, or existing insulation materials from the surfaces to ensure proper foam adhesion. Next, the spray foam insulation material is mixed and applied using specialized equipment.
Spray foam insulation comes in two primary varieties: open-cell and closed-cell. Because open-cell foam is less dense and lighter, it may expand and bend more easily. It is frequently utilized for interior ceilings and walls. Conversely, closed-cell foam is thicker and offers a more robust defense against air and moisture intrusion. It is commonly used in areas prone to moisture, such as basements or crawl spaces, and in exterior applications.
The installation crew's skills and training are essential for even application and comprehensive coverage. Environmental factors during installation, such as temperature and humidity, must be considered, as they can affect the foam's curing process. Additionally, attention to detail in sealing gaps and cracks and proper ventilation to allow for the off-gassing of chemicals are important considerations for achieving optimal results.
By understanding the installation process and the different types of spray foam insulation available, homeowners and contractors can make informed decisions to improve the energy efficiency and comfort of buildings while minimizing potential issues.
Understanding the cost dynamics is crucial when considering spray foam insulation. While the upfront costs may be higher than traditional insulation types like fiberglass or cellulose, weighing these against the potential long-term savings is essential.
Over time, spray foam's more excellent insulating qualities can significantly reduce energy costs. Because of its superb gap and crack sealing capabilities, less air leakage occurs, improving energy efficiency and lowering heating and cooling expenses. In addition, spray foam insulation's durability and longevity can contribute to savings by reducing the need for frequent re-insulation or repairs.
Several factors influence the cost-effectiveness of spray foam insulation. The size and complexity of the project, such as the area to be insulated and the accessibility of the spaces, can impact the overall cost. In addition, the type of spray foam insulation chosen (open-cell vs. closed-cell) and the thickness of the insulation layer required also play a role in determining costs.
Furthermore, local market conditions and the availability of trained professionals for installation can affect pricing. However, it's essential to weigh the possible return on investment that spray foam insulation can provide in terms of lower energy costs, more comfort, and potential improvements to the property's value as a rental.
By carefully evaluating upfront costs and long-term benefits, homeowners and building owners can decide whether spray foam insulation suits their needs and budget.
Assessing the environmental impact of spray foam insulation is essential for informed decision-making. While spray foam offers excellent insulation properties, its production and ingredients can have ecological implications. The materials used in spray foam insulation, such as polyurethane, may involve using chemicals and petroleum-based products in their manufacturing processes.
Indoor air quality is also affected by the possibility of off-gassing, which is the discharge of volatile organic compounds (VOCs) into the atmosphere following installation. Proper ventilation during and after installation is crucial to mitigate this risk and ensure a healthy indoor environment.
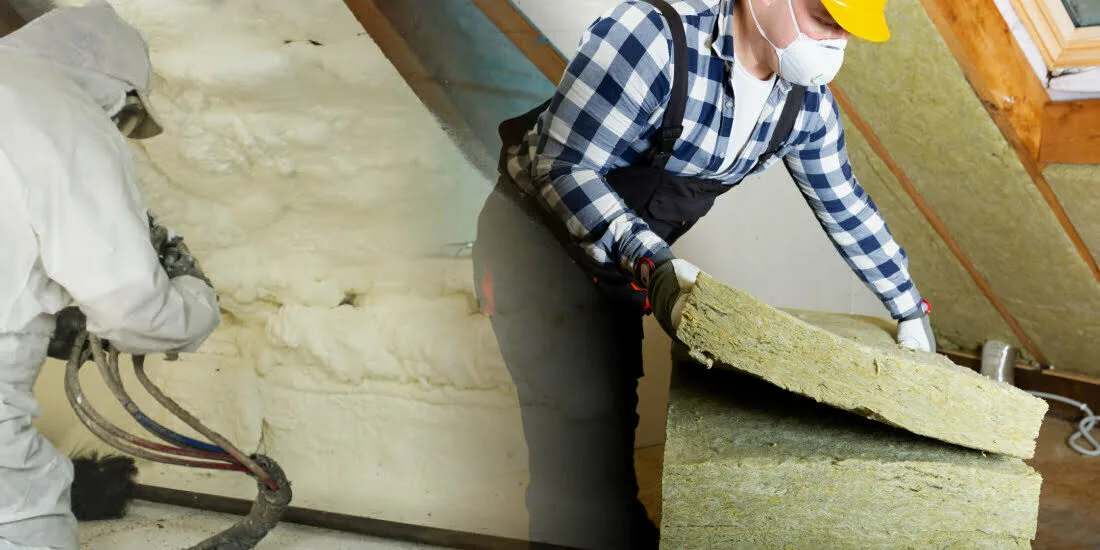
However, more eco-friendly solutions are available because of developments in spray foam technology, like formulations with less volatile organic compounds (VOC) or compounds derived from biotechnology. These eco-friendly alternatives aim to reduce the environmental footprint of spray foam insulation while maintaining its effectiveness.
When considering the environmental impact of spray foam insulation, weighing its energy-saving benefits against its potential drawbacks is essential. While the production and installation processes may have ecological costs, the long-term energy savings and improved indoor comfort provided by spray foam insulation can contribute to overall sustainability goals.
By choosing environmentally friendly formulations and ensuring proper installation practices, homeowners and building owners can minimize the environmental impact of spray foam insulation while maximizing its energy efficiency benefits.
Addressing moisture and mold issues associated with spray foam insulation is crucial for maintaining a healthy indoor environment. Even though spray foam fills in gaps and fractures well, poor installation or insufficient ventilation can cause moisture buildup and even mold formation.
A typical issue with spray foam insulation is condensation, particularly in humid climates. If moisture becomes trapped within the insulation material, it can further exacerbate mold growth and compromise indoor air quality.
Proper installation techniques are essential to mitigate moisture problems. This includes ensuring that all gaps and seams are properly sealed and providing adequate ventilation to allow moisture to escape. Installing a vapor barrier, especially in areas prone to moisture intrusion, can also help prevent condensation and moisture buildup within walls.
Routine maintenance and inspection are essential to detect and resolve moisture-related problems quickly. Homeowners and building owners should monitor humidity levels, especially in areas with spray foam insulation, and take proactive measures to maintain proper ventilation and moisture control.
By understanding the potential for moisture-related concerns and implementing appropriate mitigation strategies, homeowners and building occupants can enjoy the energy-saving benefits of spray foam insulation while safeguarding against moisture-related issues and mold growth.
Proper application of spray foam insulation comes with a set of challenges that need to be addressed for optimal results. One common challenge is achieving uniform coverage and avoiding gaps or uneven application. This requires skill and precision to guarantee that the foam is dispersed equally across surfaces and that all gaps and fractures are sealed efficiently to enhance insulation performance. No application or missed areas can compromise the effectiveness of the insulation, leading to thermal inefficiencies and potential air leakage. Also, spray foam insulation may only adhere correctly to surfaces if adequately installed, resulting in delamination or peeling over time.
Expert installation technique
Professional installation by trained experts is crucial to overcoming these challenges and ensuring the proper application of spray foam insulation. Expert trailers are equipped with the know-how to determine the precise requirements of every project, choose the best spray foam insulation, and apply it appropriately to get the best results.
Moreover, professional installers are equipped with specialized tools and equipment to facilitate the application process and address any challenges during installation. Additionally, they follow safety regulations and industry best practices to reduce the possibility of mistakes and guarantee the insulation's long-term effectiveness.
By investing in professional installation, homeowners and building owners can mitigate the risks associated with improper spray foam insulation application and maximize its energy-saving benefits. Hiring experienced professionals ensures that the insulation is installed correctly the first time, providing peace of mind and long-lasting comfort.
Spray foam insulation homeowners and contractors must understand the health and safety risks. While spray foam insulation offers numerous benefits, including improved energy efficiency and comfort, homeowners and contractors must be aware of potential health concerns.
One of the primary risks of spray foam insulation is the potential for allergic reactions and respiratory issues. Some individuals may be sensitive to the chemicals used in spray foam insulation, leading to symptoms such as coughing, chest tightness, or skin irritation. It is essential to have adequate ventilation during installation to limit exposure to these chemicals and lower the possibility of harmful health consequences.
Safety precautions should be taken both during and after installation to protect the health and well-being of occupants. After installation, occupants should allow sufficient time for chemicals to off-gas before re-entering the space.
When they receive routine maintenance and inspections, appropriate ventilation systems should also be installed to provide sufficient airflow and prevent indoor pollutants from accumulating. Ventilation systems can reduce potential health concerns and operate more efficiently.
By understanding the health and safety risks associated with spray foam insulation and taking appropriate precautions, homeowners and contractors can minimize potential adverse effects and enjoy the energy-saving benefits of this insulation method in a safe and healthy indoor environment.
Assessing the longevity and durability of spray foam insulation is essential for understanding its value as an investment in a property's energy efficiency and comfort. When properly installed and maintained, spray foam insulation is known for its long lifespan, typically 20 years or more.
Factors required
Several factors influence the longevity of spray foam insulation. Proper installation by trained professionals is critical to ensure the insulation is applied evenly and adheres securely to surfaces, minimizing the risk of premature deterioration. In addition, the longevity and resistance to moisture and other environmental conditions of spray foam insulation can be affected by its kind, whether closed-cell or open-cell.
Regular maintenance is essential to maintaining spray foam insulation's efficiency over time. This involves routinely checking the insulation for damage indicators, including gaps or cracks, and quickly fixing any problems to stop moisture seepage or air leaks.
By investing in high-quality spray foam insulation and implementing proper maintenance practices, homeowners and building owners can maximize the longevity and durability of their insulation investment. With appropriate care, spray foam insulation can provide reliable thermal protection and energy savings for many years, enhancing the comfort and efficiency of indoor spaces.
Understanding regulatory requirements and building codes related to spray foam insulation is crucial for ensuring compliance and safety in construction projects. Building codes vary by region and jurisdiction but generally include standards and guidelines for installing and using insulation materials, including spray foam.
Compliance requirements for spray foam insulation installation typically involve proper application techniques, fire safety considerations, and indoor air quality standards. For example, building codes may specify minimum thickness requirements for insulation layers or mandate the use of fire-retardant additives in spray foam formulations.
Conclusion
Meeting regulatory standards for spray foam insulation installation can challenge contractors and builders. Key consists operations include:
Ensuring proper ventilation during installation to prevent chemical off-gassing.
Maintaining fire safety measures.
Addressing moisture control issues.
Furthermore, deciphering complicated building rules and comprehending local legislation might be intimidating for individuals who need to become more familiar with the requirements. However, working with experienced professionals knowledgeable about regulatory compliance can help mitigate these challenges. We ,as expert callers, can guarantee that spray foam insulation is implemented appropriately and complies with all required standards since they know local building laws and regulations.
By prioritizing compliance with regulatory requirements for spray foam insulation installation, builders and contractors can ensure construction projects' safety, efficiency, and longevity while avoiding potential legal and financial liabilities. Compliance with building codes also helps protect occupants and the environment by promoting sustainable and safe construction practices.
Reach Out To Spray Foam Insulation Westminster
Delivering Quality Insulation Solutions in Westminster, Colorado
Call us today!